RFID production line management system plays a pivotal role in modern production lines. So how does this system work? Today we will take a closer look.
1. Project Background
In traditional manufacturing enterprises, daily management is more concentrated in product management, quality management, warehouse management. And mobile asset management, on-site personnel management, fleet management, etc. Production line management. The collection of production line information usually adopts manual collection and manual input. This manual collection and manual input method is far from accurate and has a high error rate. In addition, manual input can only be done periodically.
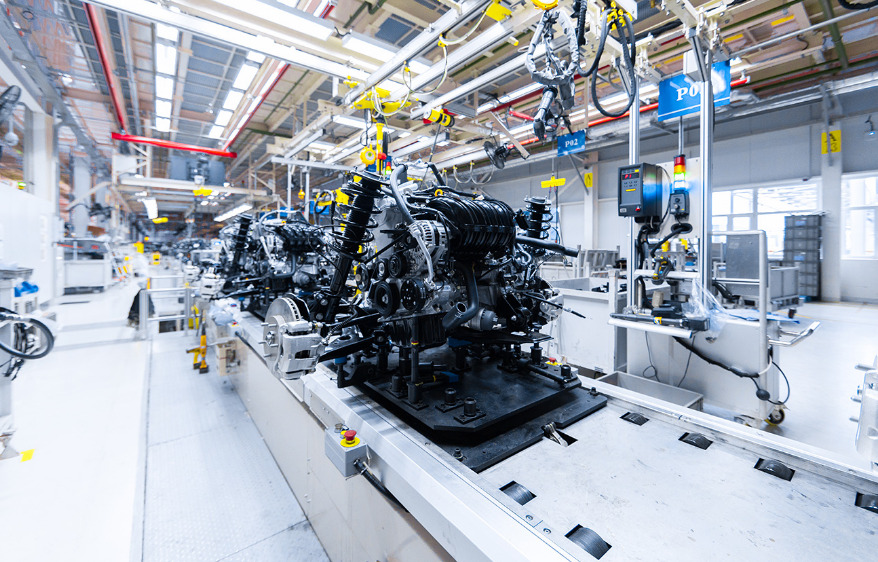
rfid Production line management 4
Not Accurate
Resulting in weekly or monthly submissions of production plans that cannot be accurate to the day. The production data in the system cannot be updated in real time, and the lag is serious. Which is not conducive to the smooth progress of the production process. And restricts the further improvement of production capacity. At the same time, manufacturing companies have realized the existence of these problems. And are trying to use emerging technologies to solve them. Currently, some manufacturing companies use barcode recognition to improve the accuracy of data entry.
However, there are still technical bottlenecks in barcode recognition:
- The work efficiency of workers is different. Which is easy to cause uneven division of labor among groups.
- It is impossible to find production abnormalities and production line bottlenecks in real time.
- Low labor efficiency and low utilization rate of actual working hours.
- Once the barcode label is not clearly printed, there will be problems such as creases and difficult identification of the barcode gun.
- Real-time tracking is impossible. And it is difficult for the management to arrange work according to the work status. If there is a problem in a certain process in the work process. It must be eliminated until the next day.
- Barcode data collection requires a dedicated team of personnel to operate. And the labor cost is high.
Requirements
Therefore, the production line management system is increasingly unable to meet the requirements of enterprises. For efficient and lean production management. While deepening the modern management concept. It is of great significance to the enterprise to build a more technical production line management system.
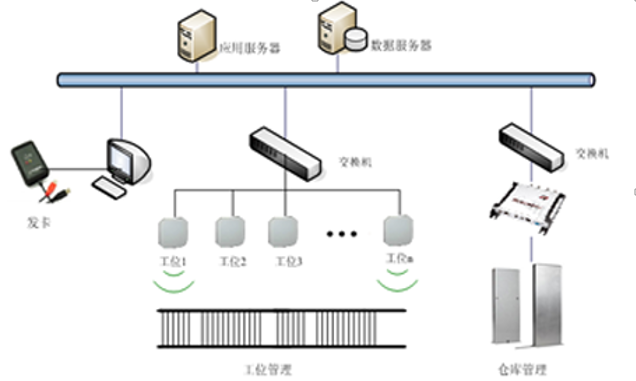
rfid Production line management 1
2. Project Definition
RFID radio frequency identification technology is an emerging high-tech technology. Which has caused changes in the field of automatic identification after barcodes. It utilizes the penetrability, long-distance transmission and wireless electromagnetic waves. To realize identification through specific protocols. Item information automatic identification technology. In the manufacturing industry, UHF (Ultra High Frequency). RFID technology essential advantages compare with the currently widely used barcode technology. It can not only read and write wirelessly at a long distance. But also have the functions of penetrating reading and high-speed mobile reading and writing. It can store more data and can also be used in harsh environments. Therefore, RFID technology is not just a simple replacement for barcode technology.
Production construction line management system is based on the computer network.
With RFID as the core
The construction meets the production management requirements of the enterprise. And aims to solve the existing problems of the enterprise. A comprehensive management system that automatically collects real-time data in the whole production process. And manages the tracking and management of batch numbers.
As a data carrier, electronic tags can play the roles of identification, item tracking, and information collection. The RFID system consisting of electronic tags, readers, antennas. And application software is directly connected to the corresponding management information system. Every item can be tracked accurately. This comprehensive information management system can bring many benefits to customers. Including real-time data collection and tracking management. Therefore, RFID technology is applied to the tracking and management of goods transfer between production lines. It can effectively prevent errors, realize intelligent production line logistics management. And greatly improve the production line management level of enterprises.
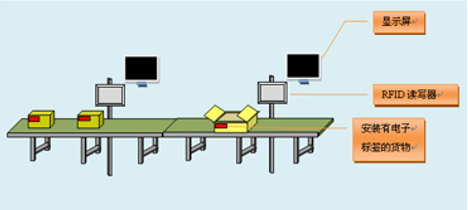
rfid Production line management 2
3. System Design
The production line management system based on RFID technology. Applies advance RFID radio frequency identification technology to production lines. Transshipment and temporary storage warehouses. And uses reusable radio frequency electronic tags. Each tag has a unique ID number and a readable and writable data area. Write the product information into the RFID electronic tag. Install the reader at the offline station of the production line and the entrance of the warehouse. Automatically write and collect the product information of each location by reading and writing the tag information. And share the data information with other IT systems, at the same time. It displayed on the screen, prompting the production line operator. So that the semi-finished products are transferred from the offline to the warehouse, temporarily stored.
3.1 Construction goals
Manufacturing production line enterprises introduce RFID, combine RFID with existing IT systems. Establish a real-time production line management system, optimize and rationally utilize resources. Increase production capacity, improve asset utilization, higher levels of quality control. And various online measurements to create greater benefit the business.
RFID provides a constantly updated stream of real-time data. Complementing the Manufacturing Execution System, the information provided by RFID. Used to ensure the correct use of labor, machines. Tools and components, enabling paperless production and reducing downtime. In addition, the production process can be controlled. Modified or even restructured in real time as materials. Parts and assemblies move through the production line to ensure reliability and high quality. All data is collected wirelessly at high speed by client computers.
Base on real-time data flow
Management systems such as ERP can mine these massive data. Conduct real-time and effective supervision of production plans and processes. RFID can provide the most accurate calculation of the man-hours required by the process. The ERP software can accurately evaluate the process and working time of each worker through RFID. And calculate the actual production capacity of each production line. Business managers can use this data to make a more accurate analysis of the company’s business capabilities.
Complete data mining and analysis. Enterprise managers can master workshop capacity, solve production bottlenecks in real time. monitor production progress in real time, and improve production processes through quality monitoring. RFID provides a basis for enterprises to achieve a balanced production line. Is compatible with enterprise ERP, SCM, MCS, etc. Combine with mainstream management systems. so that every employee in the enterprise can maximize energy efficiency.
3.2 System Network Diagram
The network diagram of this system is as follows.
The system mainly realizes the intelligent management of the entire production line. From card issuance to station management and warehouse management.
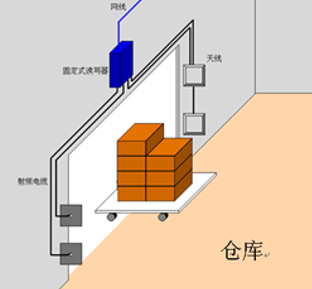
rfid Production line management 3
3.3 System flow
3.3.1 Card Issuance Management
Arrange production plans according to production orders, including production order import. Order statistics and status information transmission, production task decomposition, automatic task allocation, etc. According to the production plan to produce and issue electronic labels. And bind the electronic labels to the goods that need to be managed. And obtain information through the ERP sharing interface, write the information into electronic labels. Such as batch, box number, etc. Establish product files in the production management system. And comprehensively track the conversion process line of goods production.
3.3.2 Workplace Management
RFID readers and antennas are installed at each site. When the goods with RFID tags enter the RFID work point. the reader (writer) reads the data information stored in the electronic tag on the product. The read (write) device reads the obtained electronic data information. And directly transmits it to the logistics control management Information system. Then the management system lists the package number and batch information of the goods according to the product production information. and displays it on the display screen, prompting the production workers to perform the correct operation.
3.3.3 Warehouse management
After the goods are processed on the production line. They need to be sent from the production line to the transit warehouse. Where an RFID channel-type reading device install to realize automatic collection. Of cargo information and real-time data update in the back-end warehouse. The goods are automatically released from the warehouse in batches in the same way. Realizing real-time and efficient management of the goods.
4. System benefits
Establishing a production line management system based on RFID technology can bring the following benefits to enterprises:
1. Production data can be collected accurately and in real time.
Real-time feedback of production data is the basis for ensuring smooth production. The real-time production data of the production workshop collected by the system. Is automatically collected in real time by the RFID equipment. The RFID reader reads the specific information contained in the RFID electronic tag feeds it back to the system. The server updates the data every 5 seconds. . Through this mode of operation, the system can provide real-time production data for collection and data analysis.
2. Improve productivity on the original basis
Productivity is the focus of production management, but also the difficulty of management. If the productivity increases, it means that the output of the enterprise will increase. And the profit will also increase. The real-time production data of the production workshop is fed back to the system. Through system monitoring, the reasons that hinder the smooth flow of the production line can be found in real time. And the production bottleneck can be found in time. Through real-time data collection. The system monitors the production situation of each workshop, group. And station in real time.so as to find any abnormal situation in any production link. And solve the bottleneck that hinders the production process in time. Production efficiency.
3. Real-time tracking of order progress to ensure timely delivery
If the order is not shipped in time. It means that the company will not only be unable to make a profit but will lead to a loss. and will also affect the company’s reputation. The future development of the company has been greatly affected and hindered. Especially export enterprises are more important for the timely delivery of orders. The system starts with the customer’s order. and tracks the real-time progress of the entire production process of the product produced from start to finish. Track the order progress on the production line in real time. So as to accurately grasp the production progress of each order and achieve the purpose of timely delivery.
author:SHIJUN LI